HP findet disruptive Lösung
Der PC-Markt stagniert also, der Druckermarkt ist gar leicht rückgängig und nun stand Ramon Pastor im Jahr 2012 im europäischen Forschungs- und Entwicklungszentrum in Sant Cugat del Vallès, 17 km nordwestlich von Barcelona, mit einer Münze in der Hand und dachte bei sich: «Das ist es! Wir haben den Weg gefunden.» Er setzte sich nieder, schrieb mit seinem Team einen Businessplan, flog damit nach Palo Alto ins Hauptquartier und erklärte seinen Vorgesetzten, mit welcher Technologie HP in den Zukunftsmarkt des Additive Manufacturing einsteigen kann.
«Multi Jet Fusion» nennt HP seine neu erfundene 3D-Druck-Technologie. Und auch wenn Ramon Pastor einer ist, der im Gespräch seine Worte mit Bedacht und Sorgfalt wählt, muss er – wenn er über die neue Technologie erzählt – immer wieder auf das Wort «disruptiv» zurückgreifen und das will etwas heissen. «Wir strebten von Anfang an eine disruptive Lösung an», sagt er zum Beispiel.
HP versucht, Bewährtes und Neues zu kombinieren
Das disruptive Element war Teil des Entwicklungsplans bei HP. Um die Messlatte noch höher zu legen, war ein zweites Ziel festgelegt worden: Ramon Pastor und sein Team sollten einen Weg finden, um einen guten Teil der bestehenden HP-2D-Druckerlösung zu implementieren. Denn dies würde die Entwicklungszeit und die Entwicklungskosten erheblich senken. Ausserdem hatte sich gezeigt, dass sich die hauseigenen Druckköpfe bei anderen 3D-Drucker-Herstellern bereits hervorragend bewähren.
Man kann sich leicht vorstellen, dass diese beiden Kriterien das Forscherteam um Ramon Pastor an den Rand der Verzweiflung bringen konnten. Doch der gegenteilige Fall scheint eingetreten zu sein, die beiden grossen Kriterien schienen die Forscher und Entwickler anzuspornen. «Und wir haben tatsächlich auf fast schon elegante Art und Weise das disruptive Element und Teile der bestehenden 2D-Technologie zusammengebracht», sagt Ramon Pastor.
Der schläfrig gewordene 3D-Druckermarkt
Während der Druckkopf bereits vorhanden war, bot die Suche nach dem disruptiven Element erheblich mehr Schwierigkeiten. Aber ohne dieses Element wäre HP kaum mit einem 3D-Drucker auf den Markt gekommen. Denn nur eine wirklich umwälzende Technologie konnte die generativen Verfahren aus seiner Ecke holen, in die sie sich selber manövriert hatten: die Dienstleistungs-Ecke des Prototypengeschäfts und der Kleinserien.
Zwar wurden bestehenden Verfahren durchaus verbessert; die Qualität der Bauteile stieg, neue Materialien kamen im Monatstakt auf den Markt und sogar neue Verfahren wurden eingeführt, so dass man inzwischen unter achtzehn verschiedenen auswählen kann. Dass man noch erheblich an der Druckgeschwindigkeit feilen konnte, war nebensächlich geworden. Es schien zu genügen, dass man mit den additiven Verfahren Teile herstellen kann, die mit konventionellen Verfahren nicht möglich sind. HP dachte aber von Anfang an in grösseren Dimensionen.
(Bild Ramon Pastor: Eugen Albisser, Technik und Wissen)
Bis zu 30 Millionen Tropfen pro Sekunde und Druckkopf: Diese Anzahl an Tropfen inklusive ihrer Satellitentropfen muss man kontrollieren können. Und noch viel mehr die Temperatur an jeder Stelle des Bauteils und des Bauraums. Die «Multi Jet Fusion»-Technologie kann aber noch viel mehr.
(Quelle: HP)
Die Schwierigkeit: Thermik in den Griff bekommen
«Bis zu zehn Mal schneller und dies zum halben Preis». Der Satz dürfte die Konkurrenz zum Grübeln bringen – und auch viele Anwender der additiven Verfahren. Denn eines ist klar: Wer dieses Versprechen einhalten – und dazu noch die gleiche Qualität liefern kann wie die vergleichbaren Konkurrenzprodukte –, der hat sich einen Vorsprung herausgeholt.
Das Geheimnis hinter der höheren Druckgeschwindigkeit zum tieferen Preis liegt natürlich in der von HP entwickelten «Multi Jet Fusion»-Technologie. Sie basiert auf der Inkjet-Technologie von HP und es werden sogar die gleichen Inkjet-Druckköpfe benutzt wie beim 2D-Druck.
Dennoch erstaunt, dass es HP gelingt, auch beim 3D-Druck die immense Anzahl von 30 Millionen Tropfen pro Sekunde pro einzelnem Zoll des Arbeitsbereiches aufzubauen. Denn nicht nur die aus der Düse fallenden und etwas seitlich abgelegten Satellitentropfen müssen akkurat kontrolliert werden können, sondern auch die Thermik.
(Quelle: HP)
«Wenn man eine ganze Schicht in einem Arbeitsgang druckt, dann spielen viele Einflüsse eine Rolle, aber die Temperatur ist sicherlich jene, die am schwierigsten zu handhaben ist», sagt Ramon Pastor. «Man muss die volle Kontrolle über die Temperatur haben, und zwar jederzeit und überall: im Druckkopf und an jeder Stelle des gedruckten Teiles. Daher sind wir auf ein Closed-Loop-System angewiesen, das in Echtzeit Korrekturen durchführen kann und sich also dynamisch justiert. Wir haben eine riesige Anzahl an solchen Closed-Loop-Systemen mit Sensoren und Aktoren. Diese Komplexität ist ungeheuer schwer herzustellen, was ein Nachteil war bei der Entwicklung – und nun ein Vorteil, weil man es nicht so schnell kopieren kann.»
Offene Plattform für Materialien
"Wir wussten, dass wir diesen Nachteil der Materialvielfalt haben werden beim Verkaufsstart", sagt Ramon Pastor, «und deshalb setzen wir nicht wie andere Hersteller auf die Karte «eigene Materialien», sondern werden das exakte Gegenteil davon anbieten.» Zwar wird momentan vor allem mit schwarzem PA12 gedruckt, doch eine für alle Firmen offene Plattform soll helfen, so schnell wie möglich an neue Materialien zu kommen.
Dazu wurden zuerst einige Partner aus dem Chemieumfeld gewählt wie Lehmann & Voss, Arkema, BASF oder Evonik, welche die Materialentwicklung vorantrieben. Später soll die Plattform offen werden für alle Drittparty-Hersteller, was dem 3D-Druck in Sachen Materialvielfalt zu einem wirklichen Durchbruch verhelfen könnte.
Überhaupt scheint HP keine Berührungsängste zu haben. Nicht nur bei der Materialentwicklung sind viele Partnerfirmen dabei, sondern mit BMW, Siemens, Johnson & Johnson oder Nike sind Konzerne dabei, die als Partnerfirmen die Geräte im industriellen Einsatz testen und so bei der Weiterentwicklung helfen.
(Quelle: HP)
Bei den neuen 3D-Druckern von HP handelt es sich um ein komplettes Produktionssystem, zu dem auch eine zweite, separate Station gehört.
1. Druckgeschwindigkeit
Momentan gilt die um bis zu 10-mal höhere Geschwindigkeit mit 30 Millionen Tropfen pro Sekunde pro einzelnem Zoll des Arbeitsbereiches als Gradmesser für andere Technologien.
2. Schmelz- und Detailmittel
Schmelz- und Detailmittel von HP funktionieren mit der HP Multi-Jet-Fusion-Technologie und -Materialien, sodass feine Details und Massgenauigkeit sichergestellt werden.
3. Thermische Überprüfung
Durch eine genaue thermische Überprüfung jeder einzelnen Schicht können Voxel für Voxel schon im Vorfeld Anpassungen vorgenommen werden, um die gewünschte mechanische Eigenschaften zu gewährleisten.
4. Interne Qualitätsprüfungen
Interne Qualitätsprüfungen, deren Ergebnisse auf einem Touchscreen angezeigt werden, minimieren Fehler und ermöglichen eine einfache und genaue Überwachung des Jobfortschritts.
5. Mischung und Bereitstellung von Materialien
Automatisierte Systeme zur Mischung und Bereitstellung von Materialien unterstützen bei der Optimierung des Workflows.
6. Entpackungs- und Materialsammelsystems
Dank des integrierten Entpackungs- und Materialsammelsystems (einschliesslich einer Laminarhaube) ist kein zusätzlicher Platz für das Entfernen von Teilen erforderlich.
7. Schnellkühlung
Das HP Jet Fusion 3D-Modul für die Schnellkühlung verringert die Kühlzeit, sodass Teile schneller fertig werden und innerhalb eines Tages mehr Teile hergestellt werden können.
8. 3D-Baueinheit für die Kühlung
Die HP Jet Fusion 3D-Baueinheit (im Drucker enthalten) wird für die Kühlung direkt nach dem Abschluss des Auftrages verwendet, wodurch kontinuierliches Drucken und eine maximale Produktivität möglich sind.
9. Material: branchenführende Wiederverwendbarkeit
Firmen können die Kosten der Teile mithilfe kostengünstiger Materialien erheblich reduzieren: Einerseits durch die offene Materialplattform, anderseits durch eine branchenführende Wiederverwendbarkeit.
HP konnte auf dem Entwicklungsweg zum 3D-Drucker vom immensen Knowhow aus dem 2D-Geschäft profitieren. Doch beim Verkaufsnetz mussten sie sich für die zusätzliche Dimension das Knowhow extern holen. In der Schweiz ist dies die Firma SGSolution AG. Ein Gespräch mit CEO Martin Affolter.
«Wir bieten HP das fehlende CNC-Umfeld»
Martin Affolter, CEO der Firma SGSolution AG in Gränichen, kennt das europäische Forschungs- und Entwicklungszentrum von HP in Sant Cugat del Vallès inzwischen ziemlich gut. Er war bei der ersten Präsentation für das europäische Publikum in Barcelona eingeladen und war mit potenziellen Kunden schon dort, um die Drucker im Einsatz zu zeigen. Dort konnte er sich auch mit dem HP-Spirit vertraut machen. Es ist ein Silicon-Valley-Spirit ohne Rutschbahnen, aber dennoch mit einem lockeren und gepflegten «make it matter»-Geist. Martin Affolter mag diesen Spirit und er ist zudem überzeugt, dass HP mit den neuen Geräten den 3D-Druckermarkt verändern werden. Er ist HPs Mann für den Schweizer Markt. Seine SGSolution AG wurde unter mehreren Anwärterfirmen ausgesucht, um die 3D-Drucker in der Schweiz zu verkaufen.
Technik und Wissen: Herr Affolter, wie kommt es, dass HP mit seinem immensen Netzwerk in den einzelnen Ländern ein neues, zusätzliches Verkaufs- und Servicenetz aufbaut?
Martin Affolter: HP fehlt aus historischer Sicht das CNC-Umfeld. Sie suchten daher – auch in der Schweiz – eine feste Grösse, die 3D-Drucker in die Industrie verkaufen kann. Durch unseren Hintergrund und unser Wissen in und um die Fertigungsindustrie haben wir alles, was sie suchten.
Ihr Unternehmen ist spezialisiert auf den Verkauf, Handel und Unterhalt von modernen Hightech-Industrie 3D Scanner und Sie sind auch sonst im 3D-Umfeld bereits zu Hause. Wie wichtig war dieser Punkt für HP?
Wir gehören in der Schweiz zu den Pionieren, was das 3D-Umfeld anbelangt und das half sicherlich. Aber HP war auch der Unterhalt wichtig und ich darf sagen, dass die SGSolution AG oft gerühmt wird für ihren technischen Support.
Können Sie bereits etwas über den Anschaffungspreis der Drucker sagen?
Der Preis für die End-to-End-Lösung des HP-3D-Druckers liegt bei 270’000 Franken, während vergleichbare Anlagen rund eine halbe Million Franken kosten.
Was bei den Druckern auf den ersten Blick auffällt: Dass es sich um ein komplettes Produktionssystem handelt, zu dem auch eine zweite, separate Station gehört. Wozu dient sie?
Diese «Processing Station» kann mehrere Aufgaben übernehmen – zum Beispiel die Teilereinigung. Bisher war die Reinigung sehr aufwändig beim SLS-Verfahren und pulvertechnisch gab es keine saubere Lösung. HP stellt für diesen Zweck eine separate Einheit zur Verfügung. Man führt den Bauraumwagen vom Drucker in diese «Processing Station», wo das Pulver – sauber getrennt also – halbautomatisch abgesaugt wird. Danach wird das alte Pulver mit frischem gemischt und der Bauraum wird so für einen neuen Druckjob bereitgestellt.
In der separaten Einheit ist auch ein Kühlsystem integriert. Welche Vorteile bietet es?
Beim SLS-Verfahren hat man das Problem, dass die Abkühlungszeit etwa so lange dauert wie die Druckzeit. Wenn also der Druckvorgang 50 Stunden dauert, dann muss man mit 50 Stunden Abkühlungszeit rechnen. Da wir nun erheblich schneller drucken, verkürzt sich natürlich die Abkühlzeit ebenso, im genannten Beispiel von 50 Stunden auf gerade einmal 10 Stunden.
HP wird mit zwei Modellen auf den Markt kommen. Verfügen beide über dieses Abkühlsystem?
Das 3200er-Modell kann als Stand-alone-Lösung einsetzt werden. Sie ist zwar für den Prototypenbau gedacht, aber man kann selbstverständlich das Abkühlsystem dazu haben. Das 4200er-Modell verfügt in jedem Fall über das komplette System.
Welche Käufer sollen mit dem 4200er-Modell angesprochen werden?
Mögliche Käufer sind bestehende 3D-Druck-Kunden, die aufgrund der Wirtschaftlichkeit wechseln wollen. Wir können noch nicht gegen SLA (Stereolithografie) und MJM (Multijet) antreten in Bezug auf Genauigkeit. Der Fokus gilt der bestehenden SLS- und FDM-Technologie, wo man ebenfalls Echtteile drucken kann, dies aber zu sehr hohen Stückkosten. Mit der HP-Technologie werden wir durch den Einsatz von PA12 ausserdem Echtteile drucken können, was mit SLA/MJM durch den lichtaushärtenden Prozess nicht oder nur bedingt möglich ist, weil der Alterungsprozess zu früh einsetzt.
Die Drucker werden ab Mai 2017 anhand einer Reservierungsliste installiert. Wie ist das Vorgehen, wenn man sich bereits jetzt für die 3D-Drucker interessiert?
Den ersten offiziellen Auftritt hatten wir an der Fachmesse Prodex im November 2016 in Basel. Ende Januar 2017 waren wir an der Messe Swiss Plastics sowie im März auf der AMX-Tagung, wo wir weitere Einblicke in diese Technologie gewährten. Anfang April wurde bei uns ein Demo-System installiert, auf dem wir bereits etliche Live-Demos und Kundenversuche durchführten. Die ersten Auslieferungen erfolgen wie erwähnt ab Mai 2017.
«Sie haben vieles richtiggemacht»
Die Firma prodartis AG ist ein 3D-Druck-Dienstleister, welcher Serienteile additiv in hoher, spritzgussnaher Qualität herstellt. Ihre eingekauften Standard-Drucker rüsten sie selber auf, um sie an die eigenen Bedürfnisse nach Qualität und Produktivität anzupassen. Ralf Schindel, Geschäftsführer der prodartis, ist einer, der sich gezwungenermassen vertieft mit den neusten Erzeugnissen der 3D-Drucker-Hersteller auseinandersetzt. Auch mit den neuen Druckern von HP.
Ralf Schindel ist kein Unbekannter in der Schweizer 3D-Druck-Szene. Seine Firma prodartis in Appenzell gilt als Vorzeigeunternehmen, wenn es um die Serienproduktion generativ hergestellter Produkte geht, die einen sehr hohen Qualitätsgrad aufweisen. Während viele Dienstleister noch im Rapid Prototyping und Kleinstserien verharren, erkannte er schon früh, dass das Prototypengeschäft nur ein Zwischenschritt sein konnte – und sich die Verfahren mit der Spritzgusstechnik und auch anderen Fertigungsverfahren messen müssen.
Dennoch begann auch Ralf Schindels 3D-Druck-Karriere mit dem Herstellen von Prototypen. Der Mitbegründer des Institutes RPD der ISG (Ingenieurschule St. Gallen), heutige Fachhochschule St. Gallen (1996) und ehemaliger Institutsleiter irpd der inspire AG, war mit dabei, als die ersten Kunststoffteile in der Schweiz mit einer Lasersinteranlage Schicht für Schicht aufgebaut wurde.
Man forschte und erfüllte nebenbei Kundenaufträge. Doch irgendwann wurde klar, dass beides zusammen in professioneller Art nicht mehr ging. Ausserdem zeigte sich für Schindel deutlich, dass der Seriendruck von Bauteilen mit der SLS-Technologie ein eigenständiges Business sein konnte. Im 2013 gründete Schindel zusammen mit seinem Geschäftspartner Beat Bossart im Oktober 2013 die Firma prodartis.
Bauteile herstellen, die man mit anderen Technologien nicht herstellen kann
Heute verfügt die Firma über mehrere 3D-Drucker, die auf die Bedürfnisse der Firma angepasst wurden, oder wie Ralf Schindel es nennt: «Es handelt sich um gepimpte SLS-Technologie, die wir einsetzen.» Wer mit Schindel redet, der wird öfters das Wort «Qualität» hören. Aber das ist kein Wunder, denn wer die Arbeit der Appenzeller in Anspruch nimmt, der setzt nicht nur auf Qualitätsarbeit, er bekommt sie auch. Doch eine hohe, Spritzguss nahe Qualität hinzubekommen ist eine Herausforderung für die additiven Verfahren.
Eine hohe, Spritzguss nahe Qualität hinzubekommen ist eine Herausforderung für die additiven Verfahren.
«Da wir mittels schichtweisem Aufbau die Materialeigenschaften mitbestimmen, braucht es insbesondere für die gleichbleibende Qualität ein enormes Knowhow und ein eingespieltes Qualitätsmanagement», sagt Schindel. Denn da ist die Anisotropie der mechanischen Eigenschaften über X-, Y- und Z-Richtung, die zu schwankenden Ergebnissen führen kann, wenn Bauteile falsch positioniert werden. Will ein Kunde einige Zeit später ein Bauteil reproduziert haben, muss das Bauteil – da die Vernetzung des Materials in der Z-Richtung geringer ist als in der X- und Y-Richtung – exakt gleich im Bauraum platziert und orientiert werden wie das früher gefertigte.
Qualität und Prozesssicherheit ist daher für Schindel eines der drängendsten Themen, mit denen sich die Hersteller von 3D-Druckern auseinanderzusetzen haben. «Weil additiv gefertigte 10’000-er Serien keine Seltenheit mehr sind und wir uns täglich dem Vergleich der Spritzgussqualität stellen müssen, steht sie für mich vor der Erhöhung der Druckgeschwindigkeit.
Denn allein wenn ich die Möglichkeit der freien Geometriewahl nutze, mehr Funktionen in ein Bauteil konstruiere, die Stückliste reduzieren und so Werkzeuge einsparen kann und die Bauteile verschachtelt und parallel aufbaue, bin ich schon produktiver und wirtschaftlicher, als wenn ich mehrere Bauteile seriell aufbauen muss. Nehmen wir das Solar-Impulse-Teil, ein Batteriekühlsystem mit Wanddicken von 0,6 mm und einer sehr komplexen Gestalt der Kanäle: Mit keiner anderen Fertigungstechnologie hätte man dieses Teil produzieren können», sagt Schindel. Es verwundert wenig, dass Ralf Schindels Firma zusammen mit den Entwicklern von Solar Impulse für eben dieses Bauteil kürzlich einen Award an der Messe AMX in Luzern gewannen.
Schindel und seine Sicht auf die Drucker von HP
Um auf das immense Potential aufmerksam zu machen, hält Schindel Vorträge zur Serienfertigung mit den additiven Verfahren. Er ist immer auf dem neusten Stand, wenn Hersteller eine neue Maschine auf den Markt bringen. Ob von einer chinesischen Firma wie Farsoon oder den Japanern von Ricoh, die kürzlich mit neuen Druckern auf den Markt kamen. Wenn Schindel die Technologie von HP anschaut, dann kommt sie seiner Zukunftsvorstellung ziemlich nahe: «Dass ein Laserspot Spur für Spur, Fläche für Fläche selektiv abfährt, das durfte einfach nicht das Ende dieser Technologie sein», sagt er. «Für uns steht zwar Qualität an erster Stelle, aber die Produktivität ist im Wettbewerb mit den konventionellen Fertigungstechnologien immer auch ein Thema.»
«Dass ein Laserspot Fläche für Fläche selektiv abfährt, das durfte einfach nicht das Ende dieser Technologie sein»
Soll die Physik überlistet werden?
Als enormen Vorteil wertet Schindel wie HP das Thema «Materialien» angeht. Statt wie bei anderen Herstellern firmeneigenes Pulver bearbeiten zu müssen, wird die angekündigte «Open Platform» von HP allen Firmen die Möglichkeiten bieten, für die Drucker Material herzustellen.
Mit etwas Vorsicht, aber als spannenden Ansatz, sieht Schindel die «Processing Station» mit dem integrierten Kühlprozess. «Das Bauteil somit schneller aus dem Partcake (Bauteilekuchen, die im Bauraum verschmolzenen Bauteile umgeben von nicht aufgeschmolzene losem Pulvermaterial) herauszuholen, das hört sich irgendwie nach Überlistung der Physik an», sagt Ralf Schindel und lacht. «Das kann problematisch sein und zu Verzug der Kunststoffteile führen, aber wenn HP das hinkriegt, dann ist das ein weiterer Meilenstein.»
«Insgesamt muss man sagen, HPs Technologie ist ein spannender Ansatz und sie haben da vieles richtig gemacht. Sie benutzen geschickt ihren Kernprozess, also das Drucken. Und darin haben sie ein enormes Wissen als Konzern und das schafft Vertrauen!»
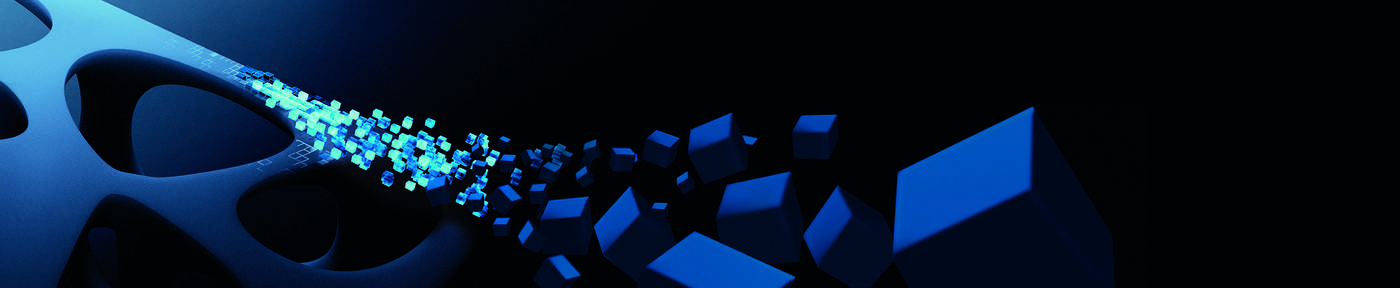
(Bild: HP)