Die Zwei-Photonen-Polymerisation – auch 3D-Laserlithografie genannt
Bei der Zwei-Photonen-Polymerisation ein (2-PP), welches auch 3D-Laserlithografie heisst, wird ein flüssiger Lack lokal begrenzt durch eine fotochemisch initiierte Polymerisation verfestigt. Das System setzt Laserlicht im nahen Infrarot mit einer Wellenlänge von 780 nm ein, für das der Fotolack transparent ist. Der Laser ist fs-gepulst und hat eine Repetitionsrate von 80 MHz. Neben der extrem hohen Geschwindigkeit arbeiten die 3D-Drucker mit einer 100 Mal höheren Präzision als beispielsweise die Stereolithografie. Erstmals können nun neue sowie erweiterte Anwendungen z.B. in der Medizintechnik, der Mikro-Optik und Photonik, Informations- und Kommunikationstechnologie, der Mikro-Mechanik oder auch in der Sensortechnik (MEMS) erschlossen werden.
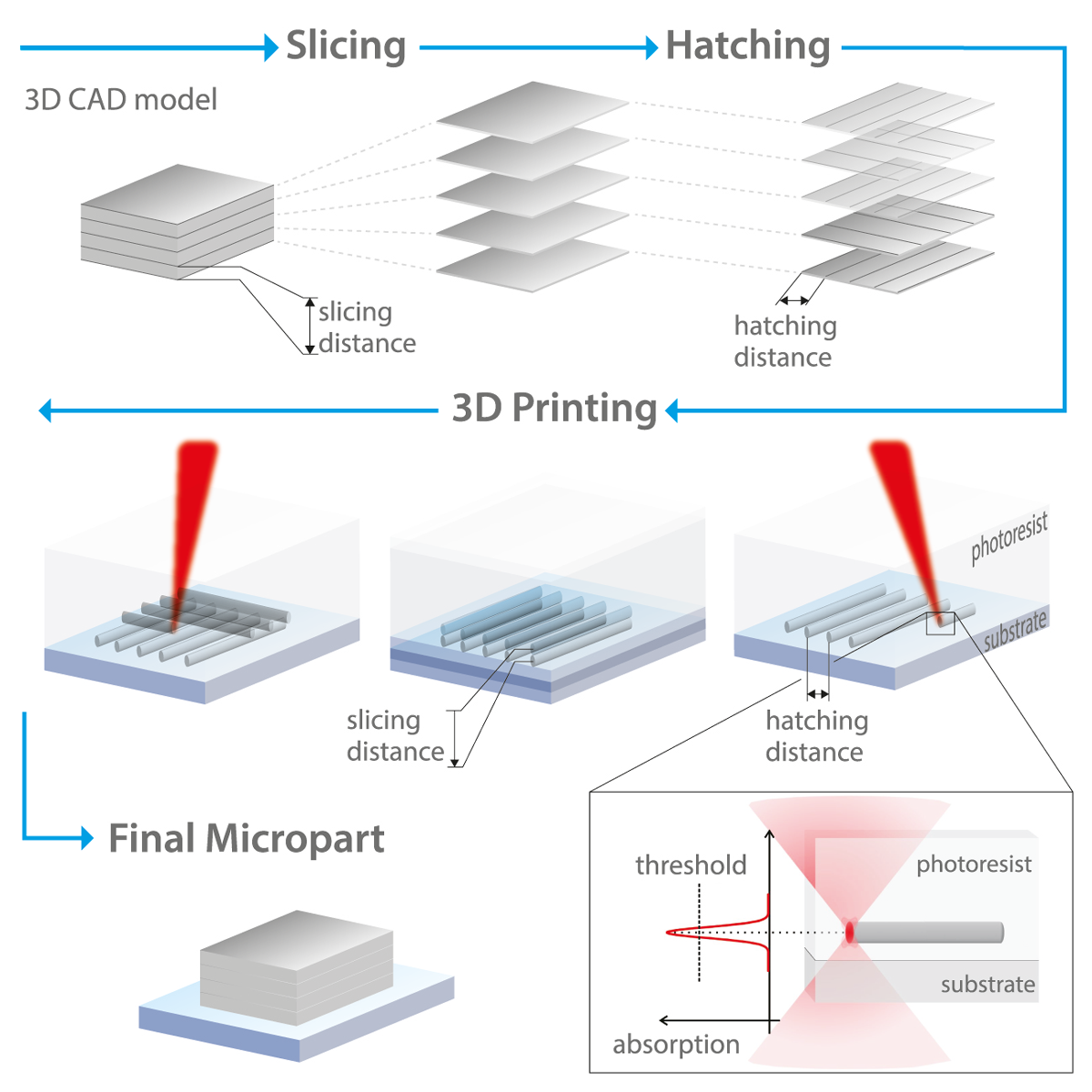
Quelle: Nanoscribe
Slicing und Hatching
Im Unterschied zur Stereolithografie wird bei der 3D Laserlithografie (auch direktes Laserschreiben genannt) mit einem Ultrakurzpulslaser im nahen Infrarot gearbeitet, um die polymeren Fotolacke mit Hilfe der Zwei-Photonen-Polymerisation auszuhärten.
Vor dem eigentlichen Druckvorgang werden die virtuellen Strukturdaten scheibchenweise unterteilt („Slicing“). Diese Ebenen bilden dann die Lagen für den späteren Druckvorgang mit einem typischen, frei wählbaren Ebenenabstand („Slicing distance“) von unter einem Mikrometer. Zusätzlich werden die Ebenen dann noch gerastert, um ähnlich einer Schraffur die Ebene vollständig mittels des Laserfokus zu belichten („Hatching“). Die fotosensitiven Materialien werden in zumeist flüssiger oder auch fester Form auf ein Trägermaterial (z.B. Glas- oder Siliziumwafer) aufgebracht. Mit den zuvor generierten Daten wird dann der eigentliche Druckvorgang gesteuert, indem der Laserstrahl die Ebenen entlang der Hatching-Linien Schicht für Schicht abrastert. Durch den Schreibprozess mit dem Laserstrahl, härten räumlich begrenzte Bereiche des Lackes vollständig aus, so dass sich nach einem Entwicklerbad ein freitragendes 3D Kunststoffobjekt herauslösen lässt.
Darauf hat man gewartet: Mikrointegration soll kommen
Überhaupt ist die Mikrointegration eines der derzeit ökonomisch bedeutendsten Forschungsgebiete der Optik. Sie bezeichnet die drastische Kosten- und Bauraumreduzierung optischer Funktionselemente. Verfügt heute beinahe jedes technische System über integrierte elektronische Schaltkreise, so werden in Zukunft auch integrierte optische Komponenten in unserem Alltag allgegenwärtig sein. Unter dem Einsatz eines 3D-Laserlithografiesystems von Nanoscribe ist Phoibos-Projektleiter Prof. Dr. Christian Koos vom Karlsruher Institut für Technologie (KIT) die optische Verdrahtung optoelektronischer Chips bereits vor ein paar Jahren gelungen. Optische Verbindungen zwischen kostengünstigen, siliziumbasierten Komponenten und anderen Materialplattformen zum Aufbau sogenannter Multi-Chip Module sind bisher schwer herzustellen.
Sie stellen höchste Anforderungen sowohl an die Positioniergenauigkeit der optischen Leiter als auch an die optische Qualität der Kontaktstellen. Unter Anwendung der sogenannten Zweiphotonen-Polymerisation lassen sich mit dem neuartigen 3D-Druckverfahren mikrometerkleine polymere Lichtwellenleiter, sogenannte photonische Wirebonds (PWB), direkt auf siliziumbasierten Komponenten realisieren. Entsprechend den jeweiligen Anforderungen können auf diese Weise optimal angepasste, optische Schnittstellen erzeugt werden, die die Basis für optische Multi-Chip Module bilden.
Nanoscribe Bibliothek Applikationen und Anwendungen
SPECTRUM OF APPLICATIONS
MICROFLUIDICS
LIFE SCIENCES
3D PHOTONIC MATERIALS
MECHANICAL METAMATERIALS
PLASMONICS
MICRO-OPTICS
MICROROBOTICS
Der Mikro-3D-Druck ist schwierig zu beherrschen und das notwendige Wissen haben selbst im konventionellen Markt tätige 3D-Druck-Hersteller nicht. Die Firma EOS ist hier eine Ausnahme. Sie ist seit längerem damit beschäftigt, ihre Lasersintertechnologie auch für die Herstellung von Mikroteilen einsetzbar zu machen. Dafür strebte EOS bereits im 2006 eine Zusammenarbeit mit der Firma 3D-Micromac an und im 2013 wurde daraus gar eine eigene Gesellschaft: die 3D-Microprint GmbH.
Mit dem DMP60 GP ist seit Kurzem die sechste Drucker-Generation der Firma auf dem Markt. Das darin eingesetzte Verfahren beruht auf der Mikro-Laser-Sinter-Technologie (MLS). Dabei wird aus sub-µm-körnigem Metallpulver Bauteile mit Schichtdicken von 1 - 5µm und bis zu 32 µm Wandstärke hergestellt – wobei für die industrielle Fertigung rund 50-90 µm Wandstärke realistisch sind. Beim DMP63GO können Materialien wie Stahl, Titan, oder auch Hochschmelzende Metalle wie Molybdenum und Wolfram eingesetzt werden. Der Nettobauraum beträgt 60 mm x 60 mm x 50 mm (X-Y-Z). «Die neue Generation der Geräte ist zurzeit bei ein paar ausgewählten Kunden im Testeinsatz», erklärt Maximilian Genz, Business Development Manager bei 3D-Microprint.
Allgemeines Funktionsprinzip des Laser-Sinterns
Quelle: EOS GmbH
Zurückhaltung bei den Industriefirmen
Noch aber zeigen sich gerade im 3D-Mikrodruck die Industriefirmen sehr zurückhaltend – obwohl man, wie 3D-Microprint auch zeigt, keine 600'000 Euro selber in die Hand nehmen muss, sondern einmal einen kostengünstigen Testversuch starten kann. «Es gibt weiterhin viele Berührungsängste», sagt Genz. «Überrascht sieht man zwar, dass hier mehrteilige, funktionstüchtige Bauteile direkt aus dem Drucker genommen werden können, ohne dass ein Montageschritt dazu kommt, und dennoch ist man sehr skeptisch, ob sich der Umstieg auf eine neues Verfahren bereits lohnt.»
Alles wächst: die Mikrotechnik-Branche und die 3D-Druck-Branche
Doch mit den 3D-Druckern für hochpräzise Mikroteile zielt 3D-Microprint und die paar wenigen anderen Hersteller auf einen bedeutsamen und wachsenden Markt. Dabei stehen nicht nur einige Trends auf ihrer Seite, welche die additiven Verfahren generell so interessant machen, wie zum Beispiel das vermehrte Eintreten für eine Nachhaltigkeit, ein verkürztes Time-to-Market, gewünschte Funktionsintegration und individuellere Produkte. Ihnen kommt auch entgegen, dass sich der Markt für miniaturisierte Produkte seit Jahren auf hohem Niveau entwickelt.
Eine neuste Umfrage des deutschen Verbandes für Mikrotechnik, dem IVAM, zeigt, dass "in den vergangenen Jahren sich die Geschäftslage der europäischen Mikrotechnik-Branche kontinuierlich verbessert hat. Der Anteil der Unternehmen, die ihre Geschäfte gegenüber dem jeweiligen Vorjahr steigern konnten, ist seit 2012 immer weiter gestiegen. Besonders in den Bereichen Aufträge, Produktion, Absatz und Export konnte die Branche deutliche Steigerungsraten verzeichnen", heisst es zusammengefasst im neusten Branchenrapport.
Aber auch die Schweiz mischt munter mit bei der Entwicklung neuer Technologien, um Mikrobauteile Schicht für Schicht zu erstellen. Alleine von der ETHZ kommen zwei Spin-offs. Die eine Firma heisst Cytosurge, die andere Scrona.
Der eine Spin-off der ETH Zürich, die Firma Cytosurge, ist in Glattbrugg beheimatet und hat inzwischen 14 Mitarbeiter – und alle Hände voll zu tun. Dabei steht nicht der 3D-Druck im Vordergrund, sondern eine neue Generation wissenschaftlicher Messinstrumente für Lösungen im Mikro- und Nanobereich, die in der Nanotechnologie, Life Sciences und Single-Cell-Biologie eingesetzt werden.
FluidFM: Völlig neues Verfahren für den Mikro-3D-Druck
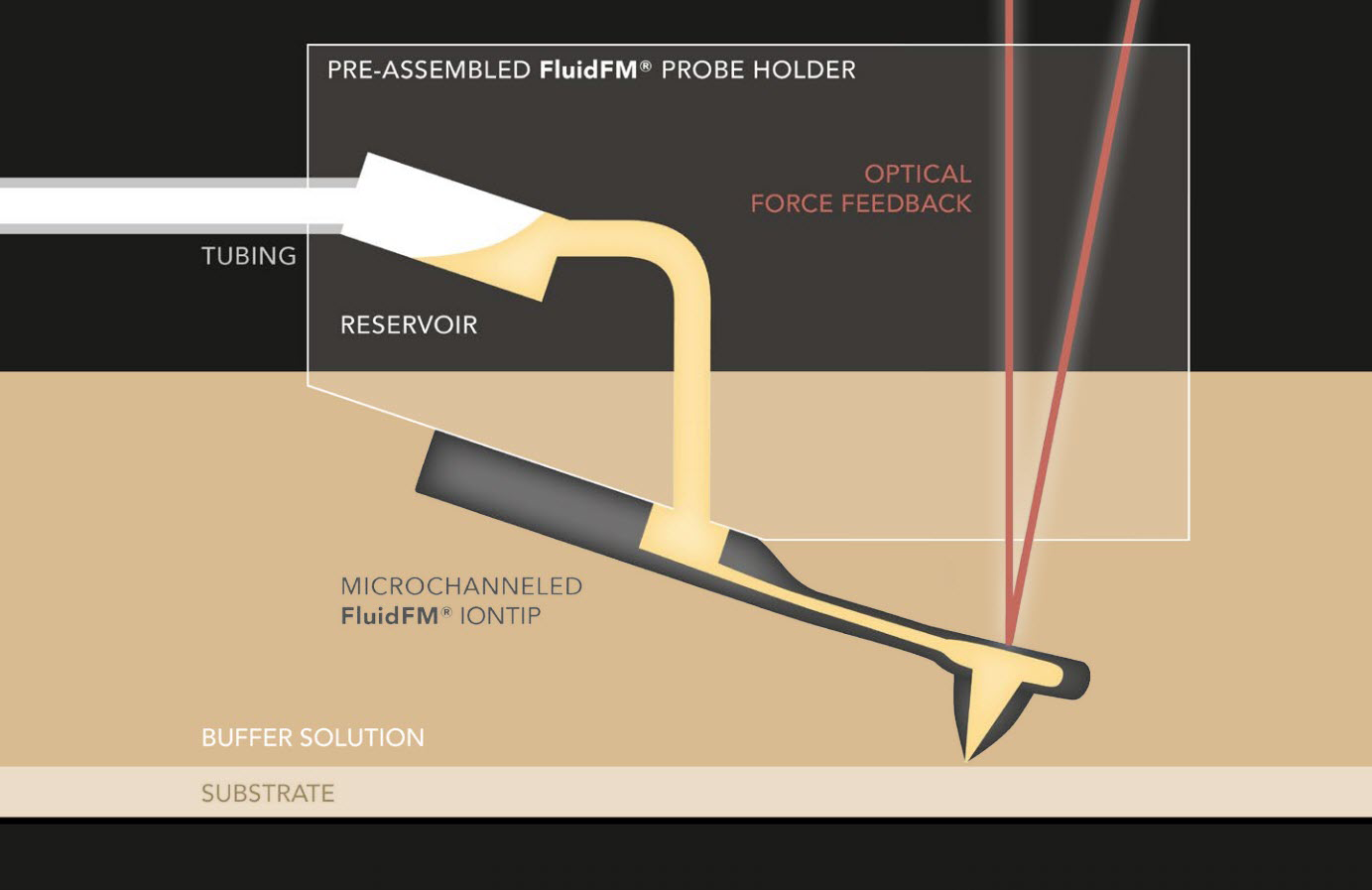
Quelle: Cytosurge
Die Basis ihrer Instrumente liefert die FluidFM-Technologie – und diese erlaubt es nicht nur, mit den Messsonden im Nanobereich zu messen, sondern über diese Pipetten mit einer nur gerade 300 Nanometer winzigen Öffnung eine metallische Ionenlösung zu senden und so dreidimensional zu drucken. Wird nun eine Spannung angelegt, kommt es an der Pipettenspitze zu einer elektrochemischen Reaktion: Das aus der Pipette austretende Kupfersulfat reagiert zu festem Kupfer, das auf einer Grundplatte aus Gold zu wachsen beginnt und der Bewegung der Pipette folgt.
Pascal Behr, erklärt die FluidFM-Technologie
Was man als nächsten Schritt macht: man geht auf die 3D-Position im Raum, wo man ein neues Voxel (ein 3D-Pixel) wachsen lassen möchte. Man lässt die Flüssigkeit raus und wartet dann bis der Voxel gewachsen ist.
In unserem Fall bringen wir Ionenflüssigkeit darauf, die reduziert wird und da wir immer noch im Hintergrund eben in der FluidFM-Technologie von einem Rasterkraftmikroskop profitieren, sehen wir den Moment, wenn dieses 3D-Pixel, dieses Voxel, gewachsen ist, weil unser Druckkopf abgelenkt wird.
Bevor wir die Nadel physisch berühren, sehen wir dies bereits und können die Nadel zurückziehen. Wir positionieren sie auf den nächsten Punkt im Raum, wo wir wiederum dreidimensionales Material additiv hinbringen möchten. Und wenn man dies richtig orchestriert mithilfe eine Computers, quasi die richtigen Pixel zur richtigen Zeit anfährt, diese wachsen lässt, gibt es am Schluss eine 3dimensionale Struktur.
Das Schöne ist, man kann es auch horizontal wachsen lassen, man braucht dazu keinerlei Support, also Unterstützungsstrukturen, die man danach mühsam entfernen muss. Was bei uns beim Drucken rauskommt, ist Metall im Mikrometermassstab und das kann sonst niemand so nach unserem Wissen.
Film: Technik und Wissen GmbH
Direkter kann man nicht drucken
Im Gegensatz zu anderen Verfahren wie jenem von Nanoscribe, deren IP-Fotolacke erst durch einen fotochemischen Prozess «metallisiert» werden, handelt es sich beim Verfahren von Cytosurge um einen direkten, template-freien Druckprozess. Und weil auch hier ein elektrochemischer Prozess zum Einsatz kommt, ist auch die Bandbreite an Werkstoffen gross, theoretisch alle Stoffe, die elektrochemisch gewonnen werden können. «Kupfer beherrschen wir inzwischen perfekt, jetzt testen wir Silber und Gold», sagt Pascal Behr, Mitgründer Cytosurge.
«Kupfer beherrschen wir inzwischen perfekt, jetzt testen wir Silber und Gold.»
Industrie ist fasziniert
Ursprünglich hatte die Firma den Plan, einen Onlineservice für die Auftragsfertigung anzubieten. «Doch wir merkten schnell, dass die Firmen noch nicht darauf vorbereitet sind, derart kleine Teile zu drucken», erklärt Pascal Behr. «Manche Firmen sind überrascht und fasziniert, wenn wir ihnen mitteilen, dass wir ihr Produkt sogar um den Faktor 10 weiter reduzieren könnten.»
Nun fokussiert sich die Cytosurge auf Industrie- und Forschungszweige, die ihre Stärken traditionell in kleinsten Abmessungen haben.
Vor allem in der Halbleitertechnologie sieht Cytosurge bereits heute einige vielversprechende Industrie-Applikationen und bietet für Forschungszwecke und wissenschaftliche Anwendungen ihren ersten Micro-3D Drucker, den FluidFM µ3Dprinter an.
«Manche Firmen sind überrascht
und fasziniert, wenn wir ihnen mitteilen, dass wir ihr Produkt sogar um den Faktor 10 weiter reduzieren könnten.»
Pascal Behr: «Wir arbeiten derzeit an der Herstellung von beispielsweise Interconnections auf Halbleiterplatten [senkrechte Halbleiteranschlüsse]. Diese werden momentan im mittleren zweistelligen Mikrometerbereich gefertigt – also zwischen 40 und 50 Mikrometer gross. Konventionelle Herstellungsmethoden haben keine Chance, kleinere Anschlüsse zu produzieren. Hier könnte dann unser Verfahren zum Einsatz kommen.» Interesse sei von Kundenseite bereits vorhanden, sagt Pascal Behr, nun gehe es noch darum, die Anlagen hochzuskalieren, um eine solche «Killerapplikation» im Milliardenstückbereich auch extrem schnell herzustellen.
Hintergrundbild Quelle: Alain Reiser, Cytosurge
Der andere Spin-off der ETH Zürich, die Firma Scrona, machte kürzlich wieder ein breites Publikum auf sich aufmerksam, weil sie ihren Erfolg im Guinness World Records Limited eintragen lassen konnten. Sie hatten das kleinste Inkjet-Farbbild der Welt gedruckt. Diesen Rekord erzielten sie mit einer neuen 3D-Nanodruck-Technologie, genannt NanoDrip-Printing.
Der Weltrekordhalter stammt aus Zürich
Das ausgedruckte Bild misst gerade mal 0,0092 Quadratmillimeter und hat Seitenlängen von 80 respektive 115 Mikrometern. «Dieses Bild ist so winzig, dass es von blossem Auge nicht mehr sichtbar ist», sagt Scrona-CEO Patrick Galliker, der mit seinen Mitgründern Julian Schneider (CTO) und Martin Schmid (CIO) versucht, die NanoDrip-Printing-Technologie weiterzuentwickeln und zu kommerzialisieren. Was man nicht von Auge erkennen kann, wird erst unter dem Mikroskop so richtig sichtbar: Es sind Clownfische auf dem Bild zu erkennen, die sich um eine Seeanemone aufhalten. Sie messen nur gerade mal rund 30 Mikrometer. Dank der verwendeten 24-bit-Farbtiefe des Ausdrucks erscheint die Unterwasserszenerie lebensecht und natürlich.
Einen Tag lang Clownfischbild drucken
Das Clownfisch zu drucken dauerte rund einen Arbeitstag. Dabei wurden drei verschiedene Materialien gedruckt und weil die im Zürcher Technopark beheimatete Scrona damals nur eine Druckdüse einsetzen konnte, musste sie jeweils wieder gewechselt werden. Um den Druckprozess stabil zu halten, musste diese beim Wechsel des Materials entsprechend ebenfalls ausgetauscht werden. Um die drei Grund-Farben rot, grün und blau perfekt zu «mischen», und den richtigen Farbton zu erzielen, musste der Druckprozess nach jedem Wechsel der Druckdüse gründlich kalibriert werden. Durch die Kalibration wurden minime Abweichungen zwischen den verschiedenen Druckdüsen ausgeglichen und so eine Kontrolle der Schichtdicke bis auf einzelne Nanometer sichergestellt.
Um die Clownfische und ihre Anemone darzustellen, wurden mehrere Lagen von roten, grünen und blauen QDs übereinander gedruckt. Die Auflösung beträgt 25‘000 dpi, der Abstand zwischen zwei Pixeln beträgt damit nur 500 Nanometer. Um die Farbtiefe von 24 Bit zu erreichen, musste die Dicke der Schichten mit höchster Präzision im atomaren Bereich festgelegt werden – und das bei jedem einzelnen Pixel. Bis anhin war es nicht einmal mit modernster Halbleiter-Technik möglich, solche Nanostrukturen, wie sie für diesen Weltrekord erzielt wurden, von derart hoher Präzision zu erschaffen. Das Bild von Scrona und den ETH-Forschern ist deshalb nicht einfach nur ein netter Gag, sondern es ist eine vielversprechende Alternative für die Herstellung von optischen Geräten oder hochauflösenden Displays auf Folien.
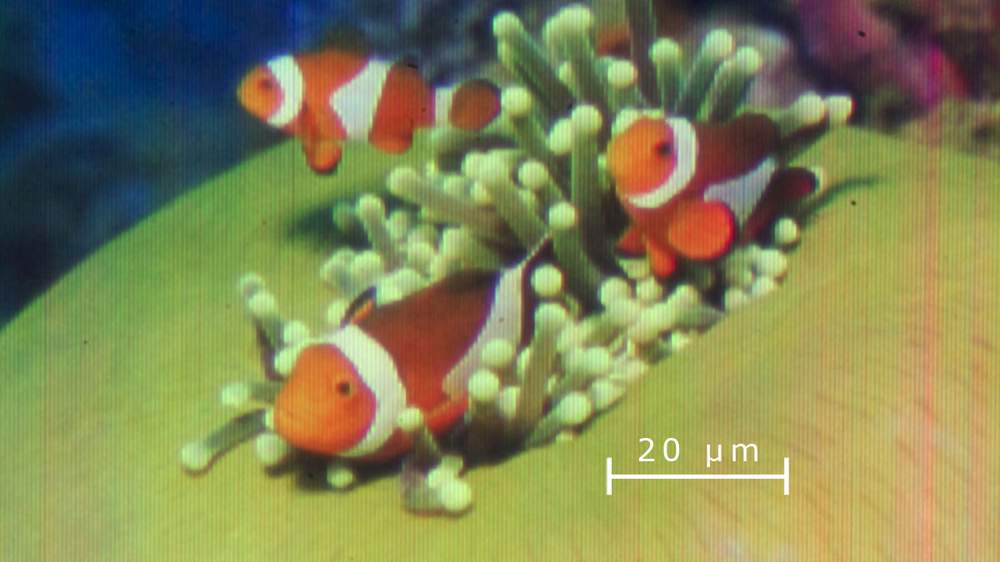
Quelle: Scrona
1 Tropfen Inkjet = 100'000 NanoDrip-Tropfen
«Das Spezielle an unserem Druckprozess ist, dass wir die Flüssigkeit nicht wie beim Inkjetdruck aus der Düse herausdrücken, sondern mittels elektrischen Kräften die Flüssigkeit herausziehen», sagt Patrick Galliker. «Der Effekt ähnelt dem von zwei sich anziehenden Magneten. Diese Kräfte erlauben es uns, im Gegensatz zum Inkjetprozess, extrem kleine Tropfen zu generieren.»
«Das Spezielle an unserem Druckprozess ist, dass wir die Flüssigkeit nicht wie beim Inkjetdruck aus der Düse herausdrücken, sondern mittels elektrischen Kräften die Flüssigkeit herausziehen.»
Um ihrem Ziel näher zu kommen und den Druckprozess industriell nutzen zu können, muss Scrona ihn nun unbedingt hochskalieren. Das ist allerdings ein physikalisches Problem. Bei einem Injektdrucker hat man vielleicht 100 Düsen. Jede Druckdüse druckt einen Tropfen von 50 Mikrometer, was etwa dem Durchmesser eines Haares entspricht – sogar etwas kleiner – und ähnlich gross ist wie das Clownfisch-Bild. Das Bild ist also so gross wie ein einziger Tropfen aus dem Inkjetdrucker. Bei unserem Druckprozess sind die Tropfen so klein, dass man Hunderttausend Tropfen braucht, für die Fläche des Bildes. «Das heisst, für dieselbe Geschwindigkeit wie eine Injektdrucker müssen wir 100’000-mal mehr Druckdüsen haben», sagt Galliker.
KTI-Projekt gibt neuen Schub
Mit einer einzigen Druckdüse zu drucken ist technisch gesehen sehr einfach. Den Einzeldruckkopf muss man sich wie einen langen Stift vorstellen – eine 10 Zentimeter lange Glaskapillare, die unten spitz zuläuft. Der Kanal wird gefühlt mit der Druckflüssigkeit, die unten durch die, nur wenige Mikrometer breite, Düse gezogen wird. Die neu entwickelten Druckköpfe werden eher flach und die Düsen sind so kurz, dass man sie kaum noch sieht. Der Druckkopf sieht aus wie ein Chip und darauf will Scrona in Zukunft bis zu einer Million Druckdüsen unterbringen. Die Entwicklungskosten dürften Millionen von Franken betragen; dank der Bewilligung eines KTI- Projektes (Kommission für Technologie und Innovation) stehen jetzt neue Mittel zur Verfügung und die Zürcher damit schon kurz vor dem Kick-Off. «Ich darf noch wenig sagen darüber, aber es ist mit drei sehr bekannten Schweizer Firmen und es wird auf eine spezifische Anwendung hingearbeitet, für welche uns vergleichsweise geringe technische Anforderungen im Weg stehen», sagt Patrick Galliker.
Hintergrundbild Quelle: Scrona
Wirtschaftlich attraktive Anwendungen entwickeln
Wie immer muss auch beim Mikro-3D-Druck das Kleingedruckte genau gelesen werden. Nicht alle Verfahren sind bisher industrietauglich und einige – wie zum Beispiel jenes von Scrona – muss man aufgrund ihrer eingesetzten Technologien eher als 2.5-D-Drucker bezeichnen. Wieder andere sind nur knapp im Mikrometerbereich, aber die Beispiele zeigen, dass sich auch die Firmen in der Mikrotechnik bereits jetzt mit dem Einsatz der generativen Verfahren auseinandersetzen dürfen – und das heisst, dass auch hier in naher Zukunft vollkommen neuartig konzipierte und noch kleinere Miniatur-Bauteile dem Markt einen neuen Schub bringen könnten. «Bereits heute sind unsere 3D- Drucker Standard in der Mikrofabrikation an Universitäten und Forschungsinstituten weltweit. Wir gehen davon aus, dass sich die generative Mikrofertigung bis in wenigen Jahren auch in der Industrie sowohl zur Prototypenherstellung als auch für Endanwendungen etablieren wird», sagt Dr. Fabian Niesler von Nanoscribe. «Aber man muss der Industrie Zeit geben, um auch unter wirtschaftlichen Aspekten attraktive Anwendungen, d.h. technisch anspruchsvolle, komplexe 3D-Mikrobauteile zu entwickeln, die in kleiner Losgrösse hergestellt werden sollen und mit anderen Verfahren entweder gar nicht zu realisieren, oder eben nur zu sehr hohen Stückkosten herzustellen sind», meint er.
«Wir gehen davon aus, dass sich die generative Mikrofertigung bis in wenigen Jahren auch in der Industrie sowohl zur Prototypenherstellung als auch für Endanwendungen etablieren wird.»